The Future of Plastic Molding Manufacturing
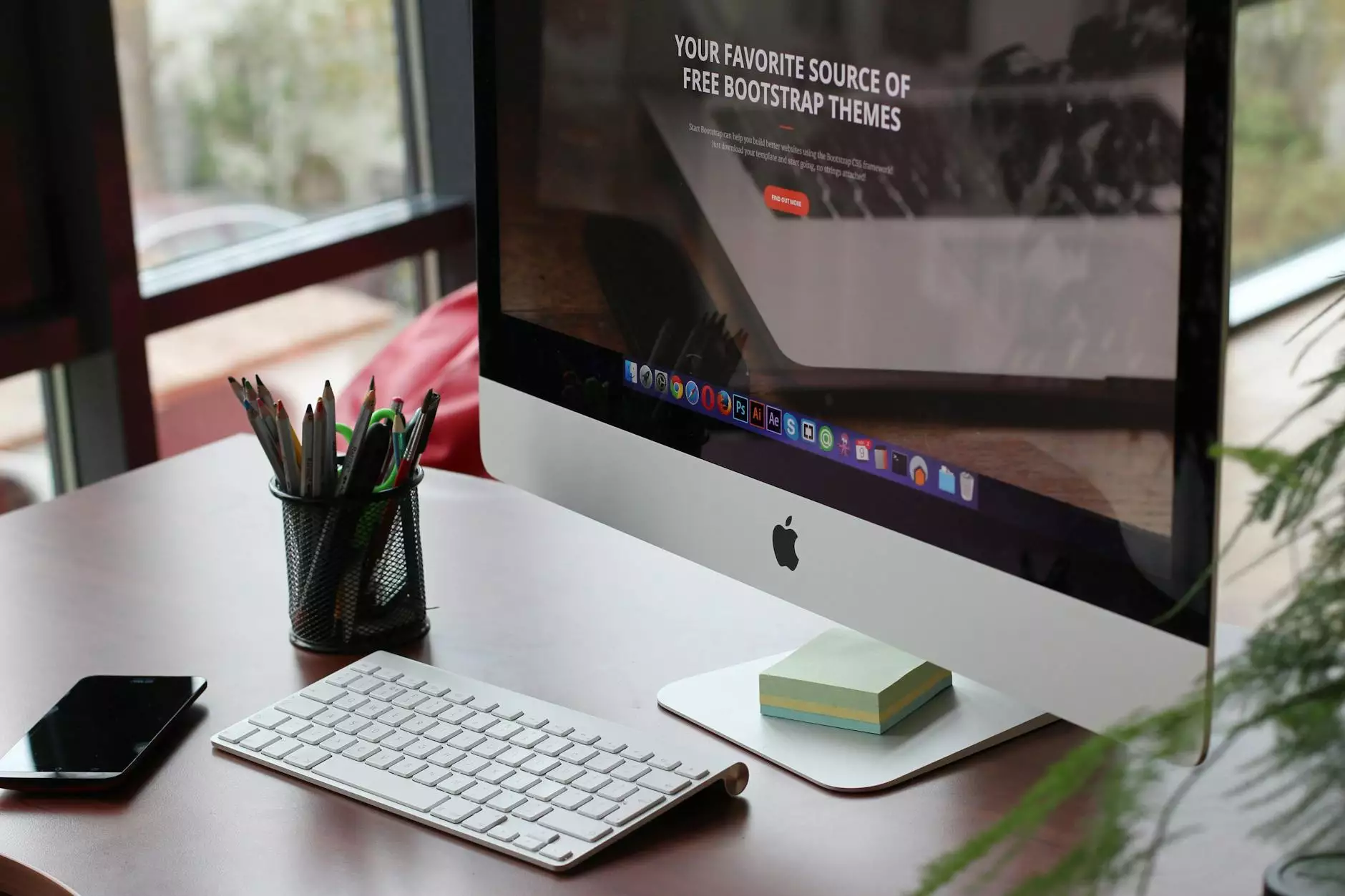
In today's ever-evolving manufacturing landscape, plastic molding manufacturing stands out as a crucial element in the production of various components and products. From consumer goods to industrial applications, the significance of plastic molding cannot be overstated. Companies that recognize its potential can gain a competitive edge, especially in the realm of metal fabrication and other complementary industries.
Understanding Plastic Molding Manufacturing
Plastic molding manufacturing refers to a variety of processes that transform plastic into specific shapes and components. This is achieved through the use of various techniques such as:
- Injection Molding: A popular method where heated plastic is injected into a mold, cooling and solidifying to form the desired shape.
- Blow Molding: Primarily used to create hollow objects, this process involves inflating hot plastic into a mold.
- Rotational Molding: A technique used for creating large, hollow items, where the mold is rotated to allow the plastic to coat the interior surface.
- Compression Molding: This involves placing plastic in an open mold and using heat and pressure to shape it.
The Benefits of Plastic Molding Manufacturing
Plastic molding manufacturing offers several advantages, making it a preferred choice for many industries:
1. Cost Efficiency
The mass production capability of plastic molding significantly reduces the cost per unit. This is particularly beneficial for companies focused on large-scale production. Furthermore, the reduced labor costs and lower material wastage contribute to overall cost efficiency.
2. Design Flexibility
One of the most appealing aspects of plastic molding is its design flexibility. Engineers and designers can create intricate shapes and patterns that are often impossible or expensive to achieve with traditional materials like metal. This flexibility not only enhances product design but also allows for innovation and creativity.
3. Durability and Lightweight Properties
Products manufactured through plastic molding exhibit a favorable strength-to-weight ratio. Plastics like polypropylene and polycarbonate provide excellent durability while maintaining a lightweight nature, making them ideal for various applications, from automotive parts to consumer electronics.
4. Environmental Considerations
As industries move toward sustainability, plastic molding manufacturing has responded with advancements in biodegradable plastics and recyclable materials. Many manufacturers are now emphasizing eco-friendly practices, thereby attracting environmentally conscious consumers.
Applications of Plastic Molding in Metal Fabrication
Within the metal fabrication industry, plastic molding plays a pivotal role. Here are some common applications:
1. Protective Components
Many metal fabricators utilize plastic molded parts as protective covers or casings for machinery and tools. These parts shield metal components from dust, debris, and corrosion, extending the lifespan of the equipment.
2. Organizational Aids
Industry often requires organizational tools that help streamline operations. Plastic molded trays, racks, and bins are used to organize metal components and tools, enhancing efficiency on the shop floor.
3. Fasteners and Connectors
Plastic molded fasteners and connectors provide lightweight yet robust solutions for joining various metal parts. They often resist corrosion better than their metal counterparts, making them a favorable choice in environments prone to rust and degradation.
Innovations in Plastic Molding Manufacturing
The landscape of plastic molding manufacturing is continuously evolving with technological advancements. Some of the latest innovations include:
1. Automation and Robotics
Automation is enhancing the efficiency and precision of plastic molding processes. Robots are increasingly employed to handle tasks such as material loading, quality inspection, and packaging, resulting in streamlined operations and reduced human error.
2. 3D Printing Integration
The integration of 3D printing with traditional plastic molding processes is paving the way for hybrid manufacturing. Companies can rapidly prototype designs using 3D printing before moving to large-scale production via molding.
3. Advanced Materials
Research into new materials is ongoing, with innovations such as carbon fiber-reinforced plastics and more robust, lightweight composites. These materials are not only more efficient but also open up exciting new possibilities for product development.
The Future of Plastic Molding Manufacturing
As the demand for custom and high-quality products continues to rise, the role of plastic molding manufacturing will become increasingly significant. Here are some future trends to watch:
1. Personalization and Customization
Consumers are demanding products that reflect their unique needs and preferences. The ability to customize molds for specific applications means that manufacturers can respond swiftly to these demands, leading to more personalized products.
2. Sustainability Initiatives
With growing awareness of environmental issues, manufacturers will increasingly adopt sustainable practices, including the use of recycled materials and energy-efficient processes. This shift will be critical in appealing to ecologically-minded consumers and meeting regulatory demands.
3. Continued Investment in Technology
Technological advancements will continue to drive improvements in plastic molding manufacturing. Investment in AI and machine learning will enable manufacturers to optimize processes, improve product quality, and reduce waste.
Conclusion
In conclusion, plastic molding manufacturing is not just a method of production; it is a transformative force in various industries, particularly in metal fabrication. Businesses that embrace this technology stand to benefit substantially from increased efficiency, reduced costs, and innovative product development. As we look towards the future, the continued evolution of plastic molding will undoubtedly shape the landscape of manufacturing and define new standards of excellence.
Explore More at DeepMould.net
For more insights and detailed discussions on plastic molding manufacturing and its applications within the metal fabricators industry, visit DeepMould.net. Stay ahead in the competitive market by understanding the pivotal role of plastic molding in manufacturing processes.