The Evolution of Silicone Prototype Manufacturers in Modern Business
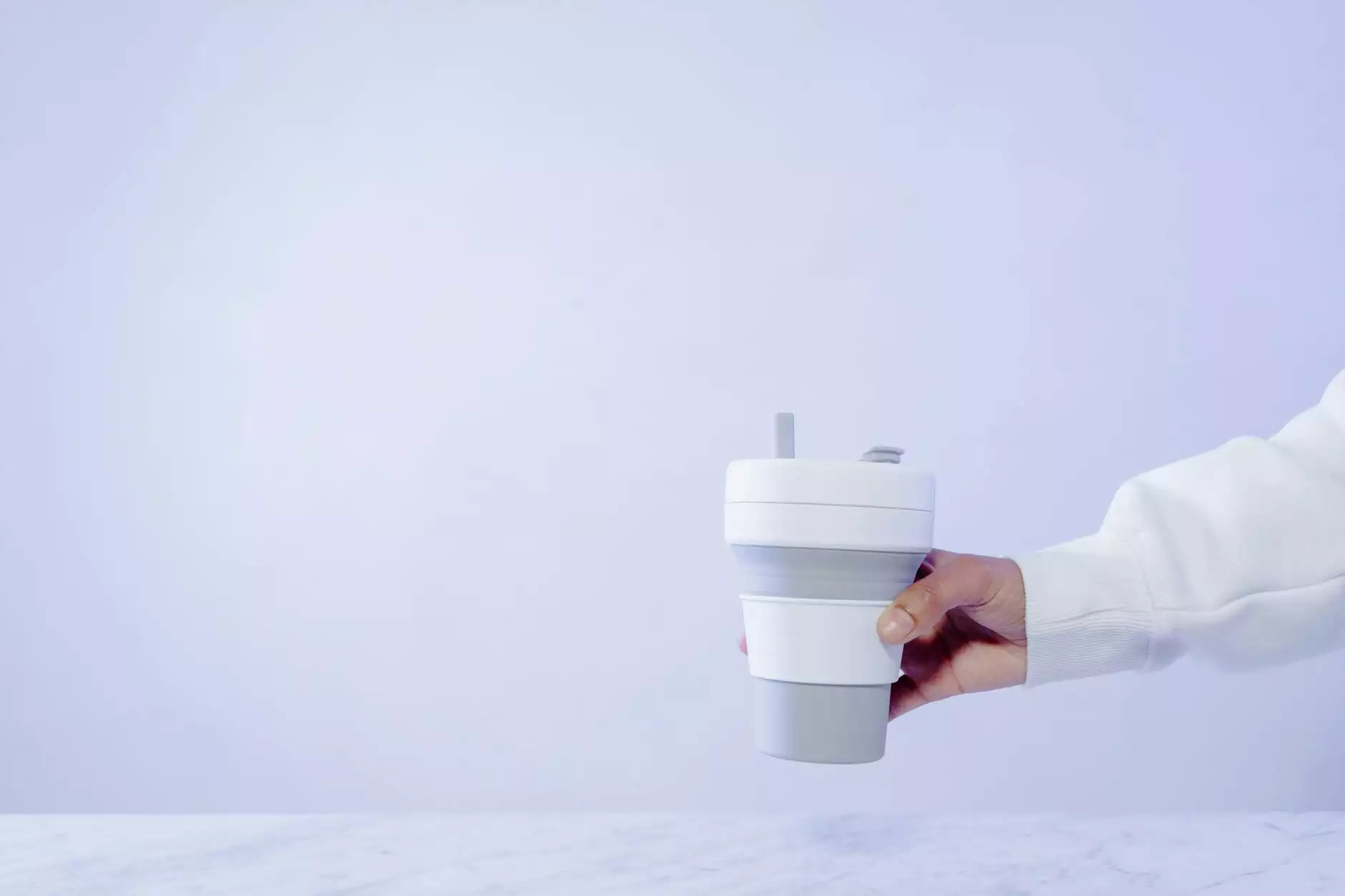
In today's rapidly evolving business landscape, silicone prototype manufacturers play a pivotal role in the development of innovative products. As technology advances, these manufacturers are at the forefront of product design, utilizing advanced techniques and materials such as silicone to create prototypes that are both functional and cost-effective. This article will delve into the significance of silicone prototype manufacturing, trends in the industry, and how companies like arti90.com are leading the way in this exciting field.
Understanding Silicone Prototype Manufacturing
Silicone prototype manufacturing involves creating models or samples made from silicone materials. These prototypes are essential for testing design concepts, functionality, and aesthetics before moving into full-scale production. Silicone, known for its flexibility, durability, and resistance to various environmental factors, is ideal for prototypes because it can closely mimic the end product's material properties.
Key Benefits of Silicone Prototyping
- Durability: Silicone models can withstand rough handling and environmental stress, allowing for rigorous testing.
- Flexibility: Silicone materials can be produced in various hardness levels, making them suitable for specific applications.
- Detail Preservation: High fidelity in reproducing intricate designs and features is achievable with silicone materials.
- Shortened Time-to-Market: Using silicone prototypes can accelerate product development cycles, enabling quicker launches.
- Cost-Effectiveness: Silicone prototyping reduces waste and allows for multiple iterations without incurring prohibitive costs.
The Process of Silicone Prototype Manufacturing
The journey from concept to silicone prototype involves several meticulously planned steps:
1. Concept Development
Everything starts with a design concept. Whether it's a new consumer product or an industrial tool, a clear concept will guide the manufacturing process. Designers sketch initial ideas and create digital models using software tools.
2. 3D Printing
3D printing technology has revolutionized the prototyping industry. Using additive manufacturing, designers can quickly transform digital models into tangible prototypes. This technology allows for rapid iteration and adjustments before settling on a final design.
3. Mold Creation
Once the prototype has been finalized, manufacturers create molds. These molds are often made from durable materials that can withstand the high pressures and temperatures involved in silicone production. Both injection molding and casting techniques are utilized depending on the complexity and volume of prototypes needed.
4. Silicone Pouring and Curing
Silicone is then poured into the mold and left to cure, a process that solidifies the material. Manufacturers are able to fine-tune the curing process to achieve different properties, such as hardness and elasticity.
5. Finishing Touches
After the curing process, prototypes undergo finishing touches that enhance their appearance and functionality. This can include painting, polishing, or adding additional components to replicate the final product.
Innovations in Silicone Prototype Technology
The field of silicone prototypes is continuously evolving. Advancements in 3D printing technology and materials science have opened new doors for manufacturers, leading to more innovative solutions for product design. Some notable innovations include:
1. Integration of Smart Materials
Manufacturers are now incorporating smart materials into silicone prototypes, allowing products to respond to environmental changes. This technology unlocks opportunities for creating *innovative consumer electronics* and adaptive products.
2. Environmentally Friendly Silicone
With a growing emphasis on sustainability, many silicone prototype manufacturers are developing eco-friendly silicone materials. These innovations not only reduce the ecological footprint but also appeal to environmentally conscious consumers.
3. Enhanced Surface Finish Techniques
Advancements in finishing techniques have led to silicone prototypes that look and feel closer to the intended final product. Techniques like silk screening and laser etching are being used for branding and surface detailing.
The Role of Silicone Prototype Manufacturers in Product Design
Product design is not just about aesthetics; it’s about functionality, usability, and feasibility. Successful silicone prototype manufacturers work closely with product designers and engineers to ensure that prototypes fulfill the intended purpose. Here's how they contribute:
1. Collaboration with Designers
Silicone prototype manufacturers often collaborate with designers during the initial stages. This cooperative approach ensures that the prototype meets all design specifications and user requirements.
2. User Testing
Prototypes made from silicone allow for thorough user testing. Feedback collected from actual users can guide further design improvements and refinements, enhancing the overall quality of the end product.
3. Iterative Design Processes
Prototyping is inherently iterative. Designers and manufacturers can repeat the prototyping process multiple times to explore different design options, which ultimately leads to a better final product.
Choosing the Right Silicone Prototype Manufacturer
Selecting a suitable silicone prototype manufacturer is crucial for the success of any project. Here are some factors to consider:
- Experience and Expertise: Look for manufacturers with a proven track record in delivering quality silicone prototypes.
- Technology and Equipment: Ensure they use the latest technologies, such as advanced 3D printing and CNC machining.
- Material Options: A good manufacturer should offer a variety of silicone materials and hardnesses.
- Customer Support: Strong communication and support from the manufacturer throughout the prototyping process can lead to better outcomes.
- Turnaround Time: Evaluate their ability to deliver prototypes within your project deadlines.
Case Studies: Successful Products Developed with Silicone Prototypes
Many successful products have been developed using silicone prototypes. Here are a few notable examples:
1. Consumer Electronics
Leading tech companies often employ silicone prototyping to test new gadgets. For instance, the ergonomic designs of different smartphone models underwent extensive testing with silicone prototypes, ensuring comfort and usability for end-users.
2. Medical Devices
The medical industry relies heavily on silicone prototypes for devices such as surgical instruments and implants. Prototyping allows manufacturers to assess user experience and safety before mass production.
3. Automotive Parts
Automakers utilize silicone prototypes for testing interior and exterior components. By creating silicone models, they can simulate performance in various environmental conditions, ensuring durability and reliability in real-world scenarios.
The Future of Silicone Prototype Manufacturing
The future holds exciting prospects for silicone prototype manufacturers. As they adapt to new technologies and market demands, we can expect to see:
1. Increased Customization
With advancements in 3D printing, manufacturers will be able to offer more personalized and customized solutions for clients, catering to specific needs and preferences.
2. Greater Emphasis on Sustainability
As businesses shift towards sustainable practices, silicone manufacturers will focus on eco-friendly materials and processes that minimize waste and environmental impact.
3. Enhanced Prototyping Techniques
Next-generation prototyping techniques, such as digital twin technology, will enable manufacturers to create digital replicas of products to test functionality and performance even before physical prototypes are made.
Conclusion
In conclusion, silicone prototype manufacturers are integral to the innovation ecosystem, bridging the gap between concept and reality in product design. With their expertise in materials, cutting-edge technology, and collaborative approach, they enable businesses to bring their ideas to life efficiently and effectively. Companies like arti90.com are at the pinnacle of this industry, utilizing state-of-the-art techniques to ensure that every product is designed with precision and care. As we embrace a future driven by rapid technological advancement, the role of silicone prototyping will only become more critical, defining the next generation of manufacturing and design.
This article has been crafted to highlight the importance of silicone prototype manufacturers in today’s market, reflecting a commitment to quality and innovation in every design.