Understanding the Significance of Metal Fabricators
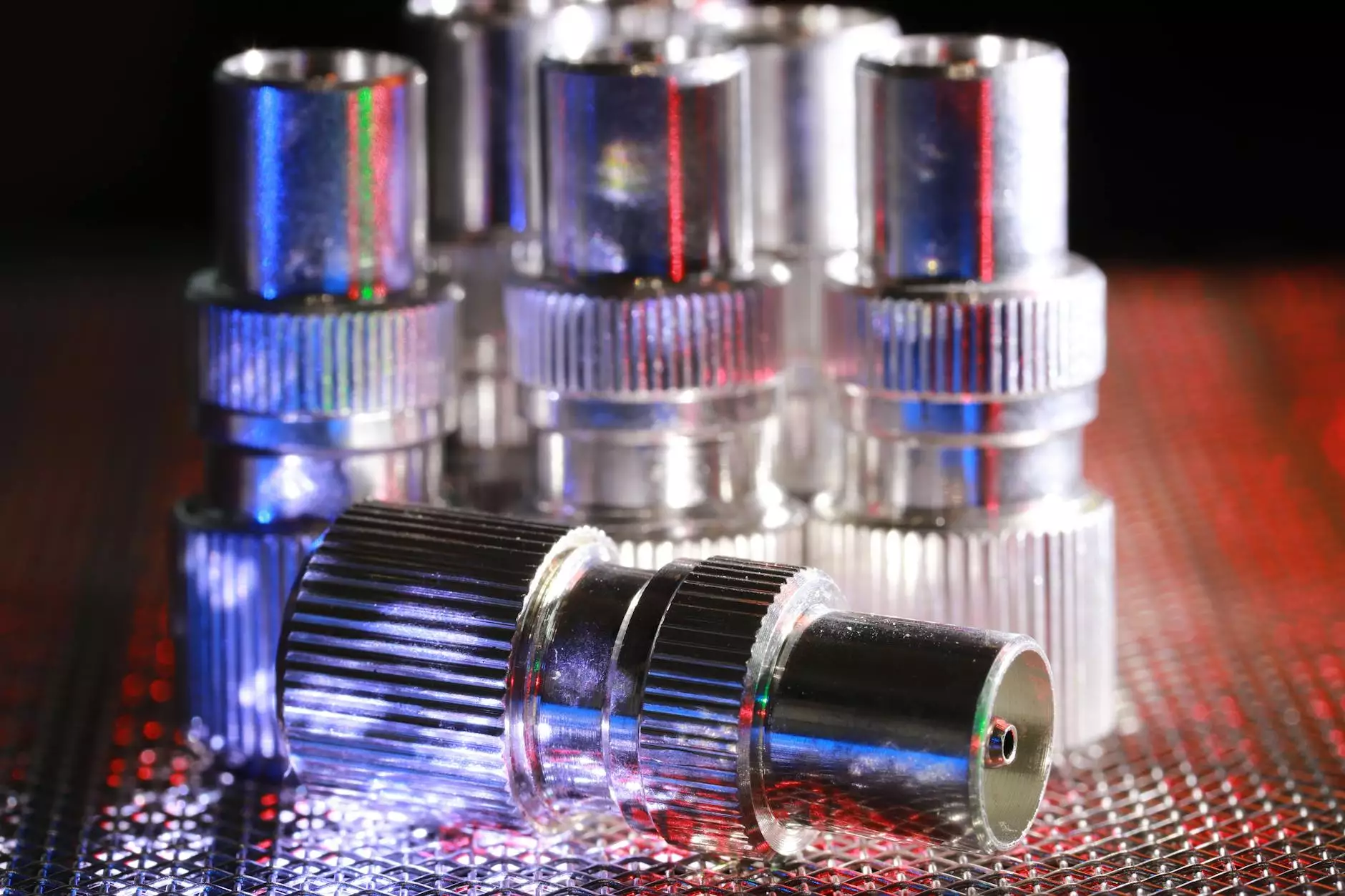
Metal fabrication is a critical process in various industries, forming the backbone of manufacturing and construction. From intricate designs to large structural components, metal fabricators play an essential role in creating the products that support modern economies.
What is Metal Fabrication?
Metal fabrication involves a series of processes that transform raw metals into finished products. These processes include:
- Cutting: The initial stage where metal sheets or blocks are precisely cut to desired dimensions.
- Bending: Shaping metal pieces into specific angles and forms.
- Welding: Joining metal parts together through high heat or pressure.
- Assembly: Combining various components into a final product.
- Finishing: Adding protective coatings or treatments for durability.
The Importance of Metal Fabricators in Various Industries
Metal fabricators are indispensable in numerous sectors, including:
Construction
From rebar to structural beams, metal fabrication is paramount in establishing frameworks for buildings, bridges, and other infrastructure. The quality of fabrication directly influences safety and longevity.
Automotive
The automotive industry relies heavily on metal fabrication for components ranging from chassis to engine parts. Precision in manufacturing ensures performance and reliability.
Aerospace
In aerospace, the need for lightweight yet durable metals is crucial. Fabricators must adhere to strict regulations and standards to guarantee safety and efficiency.
Manufacturing Equipment
Manufacturing machinery itself requires high-quality metal fabrication to ensure operational consistency and durability.
The Metal Fabrication Process Explained
Each stage of the metal fabrication process is vital, requiring a combination of skilled labor and sophisticated technology. Let's explore each in detail:
1. Design and Prototyping
The first step is to create detailed plans, often utilizing CAD (Computer-Aided Design) software. This allows for precise visualizations of the final product.
2. Material Selection
Choosing the right material is crucial, as it affects the product’s performance, weight, cost, and durability. Common materials include:
- Steel: Known for its strength and versatility.
- Aluminum: Lightweight and resistant to corrosion.
- Stainless Steel: Offers both strength and resistance to staining.
3. Machining and Cutting
Various tools, including lasers, water jets, and plasma cutters, are used to achieve precise cuts without compromising the integrity of the material.
4. Forming and Bending
Utilizing hydraulic presses and other equipment, metal sheets are shaped to meet design specifications while ensuring structural integrity.
5. Joining Processes
Welding, soldering, and riveting are common methods used to join different metal components. Techniques vary depending on the materials and required strength.
6. Surface Treatment
Finishing techniques like galvanizing, anodizing, or powder coating enhance both the appearance and durability of the metal, protecting it from environmental elements.
Choosing the Right Metal Fabricator
Selecting a reliable metal fabricator is crucial to the success of your project. Here are some key factors to consider:
Experience and Specialization
Look for a fabricator with extensive experience in your industry. Specialized knowledge can significantly affect the outcome of your project.
Quality Standards
Ensure the fabricator adheres to industry standards and certifications. This ensures that the products meet regulatory requirements and quality expectations.
Technology and Equipment
A fabricator utilizing modern technology and machinery can produce more precise and efficient work. Inquire about their capabilities and tools.
Portfolio and Client References
Review past projects to gauge their expertise and quality. Client testimonials can offer valuable insights into their reliability and service.
Environmental Considerations in Metal Fabrication
As industries move towards sustainability, metal fabricators are also focusing on reducing their environmental impact. This can be achieved through:
- Recycling: Utilizing scrap metals reduces waste and conserves resources.
- Energy Efficiency: Implementing energy-saving practices in machinery and operations.
- Eco-friendly Materials: Sourcing materials that have lower environmental footprints.
The Future of Metal Fabrication
The metal fabrication industry is evolving rapidly, with advancements in technology shaping its future. With the rise of automation, AI, and 3D printing, the potential for innovation is enormous.
Automation and Robotics
Automating fabrication processes improves efficiency, reduces errors, and lowers operational costs. Robotics can be utilized in welding, assembly, and even quality inspection.
3D Printing
3D printing continues to revolutionize the way metal parts are designed and manufactured, allowing for faster prototyping and a reduction in material wastage.
Why Choose Deep Mould for Your Metal Fabrication Needs?
When it comes to high-quality metal fabrication, Deep Mould stands out as a premier choice. With years of expertise and a commitment to excellence, Deep Mould offers:
- Custom Solutions: Tailored fabrication services to meet specific project requirements.
- State-of-the-Art Technology: Integration of the latest equipment ensures precision and efficiency.
- Dedicated Professionals: A team of skilled engineers and technicians committed to delivering top-tier products.
For more information on how Deep Mould can support your next project, visit https://www.deepmould.net/.
Conclusion
In conclusion, metal fabrication plays an essential role in a wide range of industries, and understanding its processes helps in making informed decisions about your projects. By choosing a reputable partner like Deep Mould, you can ensure high-quality, reliable metal fabrication that supports your business goals and enhances overall productivity.